HotSpot II Thermocouple Welder
The principal difference between the HotSpot II and the standard HotSpot is its heavier wire welding capability. The HotSpot II can handle wire pairs as heavy as #14 gauge. It can also close larger tubes than the standard unit and can do light duty stud welding as an aid in wire harness attachment and in insulation blanket installation.The HotSpot II operates only from AC power. A battery-powered version of the unit is not offered. Its less than #14 weight and compact design make it a very portable package.
QUICK ACTION The HotSpot II is light and portable so you can move it right to where you need to make and attach thermocouples. The actual welding time in less than a second and the short recycle interval, even at full power, will allow you to make 6 or more welds a minute.
ECONOMICAL Making and installing thermocouple junctions using DCC's HotSpot II is extremely economical. Freestanding beads can be fabricated or junctions welded to fixturing hardware or directly to the surface being sensed, at the rate of 5 to 10 a minute. There is no need for elaborate set-ups or specially trained operators. Skip the pre-planning, expense, and delays involved with purchasing thermocouples outside or having them made through another department.
EASY-TO-USE Anyone can quickly become proficient in the use of the HotSpot II. While sophisticated internally, the HotSpot II provides the operator with a firing button and a simple on/off and energy level adjustment. A weld is generated by holding the bared end of the thermocouple wire to the bead forming graphite electrode or the surface to be sensed, while pressing the firing button.
FLEXIBLE The HotSpot II welder is a dual range high-energy unit that has the versatility to provide fine control as well as the high power capability needed for heavier wires. Front panel indicators and controls allow the operator to easily monitor the status, set the energy level, and initiate a weld cycle.
THERMOCOUPLE AND FINE WIRE WELDER TL-WELD Operating Instructions The TL-WELD welder is designed for sensor manufacturers to produce commercial grade thermocouple junctions, and by users of large numbers of exposed junction thermocouples such as test and development laboratories where multipoint temperature sensing of test pieces is required. Thermocouple Welder Technical Manual. Manufacturer., Distributor Manufacturer of Hotspot portable thermocouple welder creates freestanding junctions from thermocouple wire & allows direct attachment of. Spot generates obvious advantages in the areas of. The model 300 thermocouple welder is used in conjunction with bottled ar-gon gas which acts as the purging agent. Argon flows into the weld cavity and drives out oxygen so the welding of the thermocouple can take place in an inert environment. Chromaphone 2 serial number crack. Argon, inert gas, is not a dangerous substance. Bottled gas, however, is po. The Thermocouple Welder is a compact, simple-to-use instrument designed for thermocouple and fine wire welding It is primarily designed for use by sensor manufacturers to produce commercial grade thermocouple junctions; it is ideal for producing large numbers of exposed junction thermocouples for test and development laboratories. Super smash flash 2 download chromebook. 1 Introduction JJDH thermocouple electric welder is developed by famous domestic heat treatment temperature control manufacture. It is used for welding of technical grade B, C, E, J, K, R, S, T thermocouples, as well as suitable for users who use large amount of open interface thermocouple.
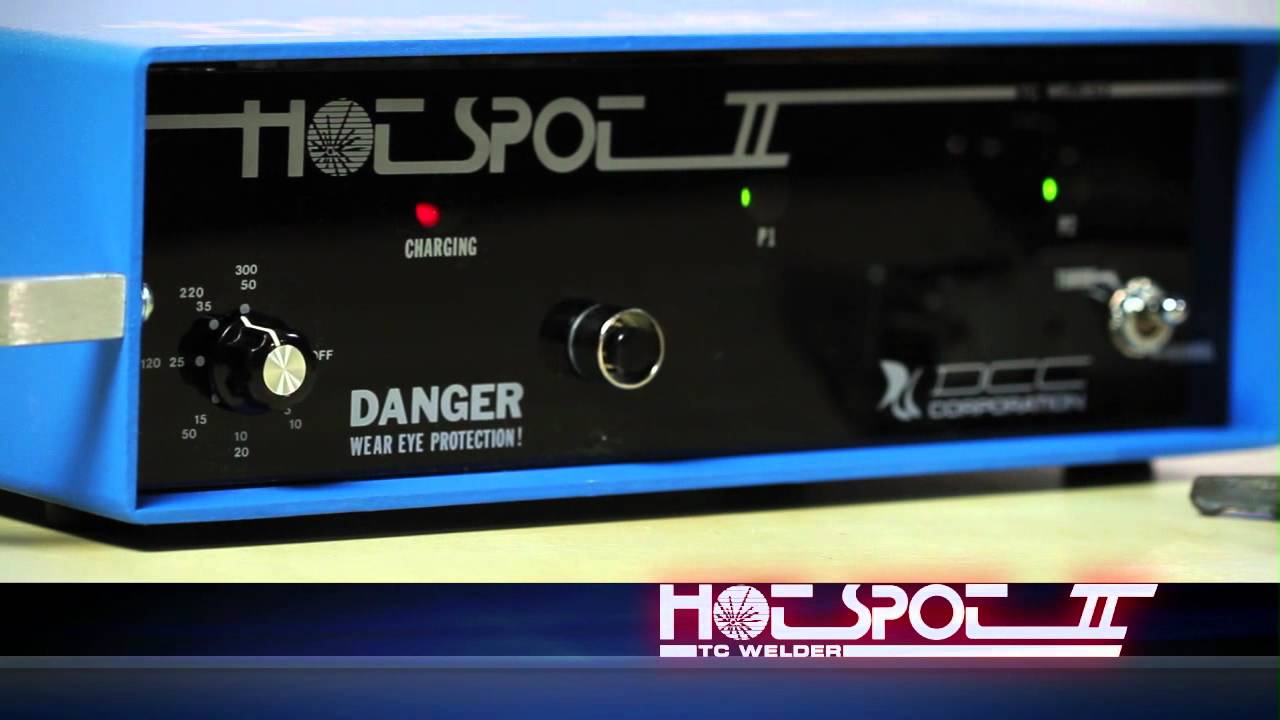
HotSpot II Specification & Price List
|

Thermocouple Welding and Soldering
Thermocouple Welding and Soldering
Hotspot Thermocouple Welder Manual Diagram
Specifically information regarding the technique, sources of error, and the pro/cons of welding vs soldering.
Why is there a special procedure/technique for welding Type T and what is the special process?
Does anyone have experience with either technique?
BACKGROUND
We have 68 Type T T/C channels located outside in New England. We currently have Omega MTC-12 connectors mounted on masts with the male connector on an umbilical to the T/Cs. The female bulkhead connector is mounted on a 4x4 enclosure. The female bulkhead mount (admittedly) does not have the specified environmental backshell. As expected we are experiencing erroneous readings and open T/Cs. The connections should not have to be undone for 20-30 years. I would like to propose removing the connectors and welding or soldering the T/C cable wires at the connection at the 4x4. Also, I would like to weld or solder the extension cables to the industrial T/C leads at the T/C peckerhead.
PS: Does anyone have a better name for the 'peckerhead'?